What is the purpose of cable insulation?
Cable insulation is an important protective material for cable conductors. It is non-conductive, used to resist electrical leakage, prevents cable conductors from contact with other conductors, and protects the conductor from environmental threats such as heat, water, and chemicals. Poor or damaged insulation may result in short circuit, electric shock, or fire.
Because the insulation of a cable is so important in determining the cable’s safety and electrical conductivity, at Keystone Cable, we ensure that all our cables are subject to passing the insulation resistance (IR) test (as part of our many tests) before product delivery to customers.
What is Insulation Resistance (IR) Test?
An insulation resistance (IR) test measures the resistance to current flow across it on a completed cable; it applies a test voltage to determine how effective the insulation is in preventing the flow of electric current out of the insulation. This is analogous to how you would pump pressurized water in a water pipe to identify leaks.
Since insulation starts to age after it is made, over time, the performance of a high quality insulation material versus one of lower quality will become more apparent. Hence it is important that after the cable is manufactured there is a good pass rate for the IR test to help ensure the longevity of your cable.
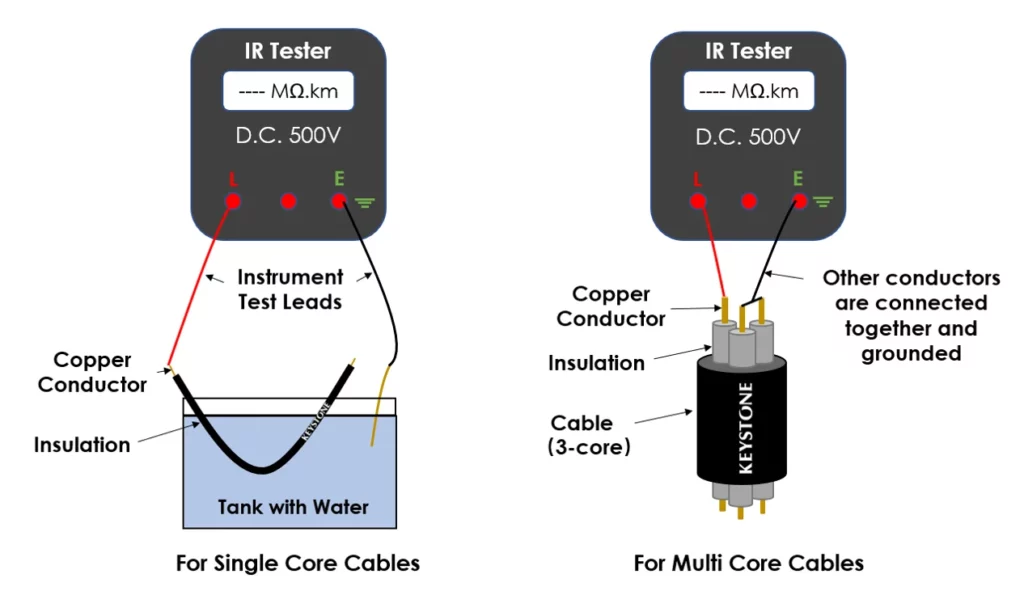
Insulation Resistance Test Process
IR test is conducted using an IR tester. The IR tester is a portable ohmmeter (MΩ.km) with a built-in generator that produces a high DC voltage. The DC voltage usually measures 500V and causes a current to flow around the surface of the insulation. This resistance reading measures leakage current; a high IR reading means very little current is escaping through the insulation and a low IR reading indicates stronger current leakage and may indicate a break in the insulation.
At Keystone’s quality control laboratory, we adhere to International Standards IEC 60502-1 for our IR tests. To pass, the cables would need to obtain a minimum insulation resistance constant Ki (refer to the table below) while tested at its maximum operating temperature (e.g. 70 °C for PVC insulated cables and 90 °C for XLPE and rubber insulated cables).

For single core cables, the cables are tested in water while for multi core cables they are tested in air. Test results will also vary for cables across different types of insulation, length of run and ambient temperature. To be certain for your cable type, feel free to check in with our team on the IR tests we perform for your cables.